Vacuum Forming
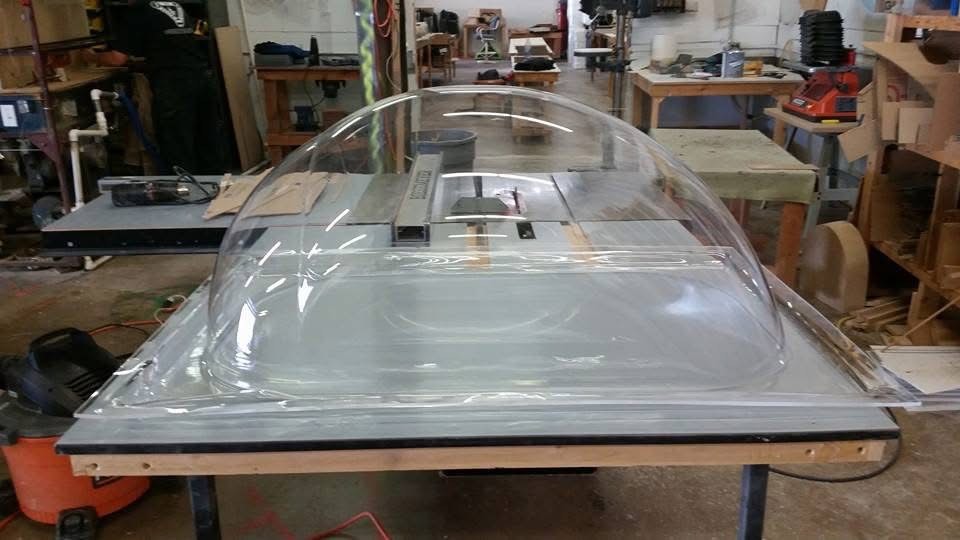
Vacuum forming is a versatile and cost-effective method for shaping plastic materials into detailed, uniform parts. In this process, a heated plastic sheet is draped over a mold, and a vacuum is applied to pull the plastic tightly around the mold, creating a precise, high-quality shape. It’s widely used in industries like automotive, industrial equipment, recreational vehicles and boats, and signage due to its ability to deliver quick turnaround times and consistent results at an affordable cost.
How Does Vacuum Forming Work?
The basic vacuum forming process typically involves the following steps:
- Material Selection: A flat plastic sheet is chosen based on the desired properties of the final product.
- Heating: The plastic sheet is heated in an oven or a heating chamber until it becomes soft and pliable. The material’s temperature is carefully controlled to ensure that it reaches the correct forming temperature without becoming too molten.
- Forming: Once heated, the sheet is stretched over a mold. A vacuum is used to draw the plastic sheet tightly around the mold.
- Cooling and Trimming: After the plastic has taken shape, it is allowed to cool and harden. The formed part is then trimmed, and excess material is recycled. The final product is inspected for quality and any additional finishing processes may be applied, such as dremmeling, bonding or routing.
Check out our materials page here to find the right material for your project!